Insights
News
Explore expert insights, industry news, press releases, and thought leadership on the latest developments shaping the future of cell and gene therapy manufacturing.
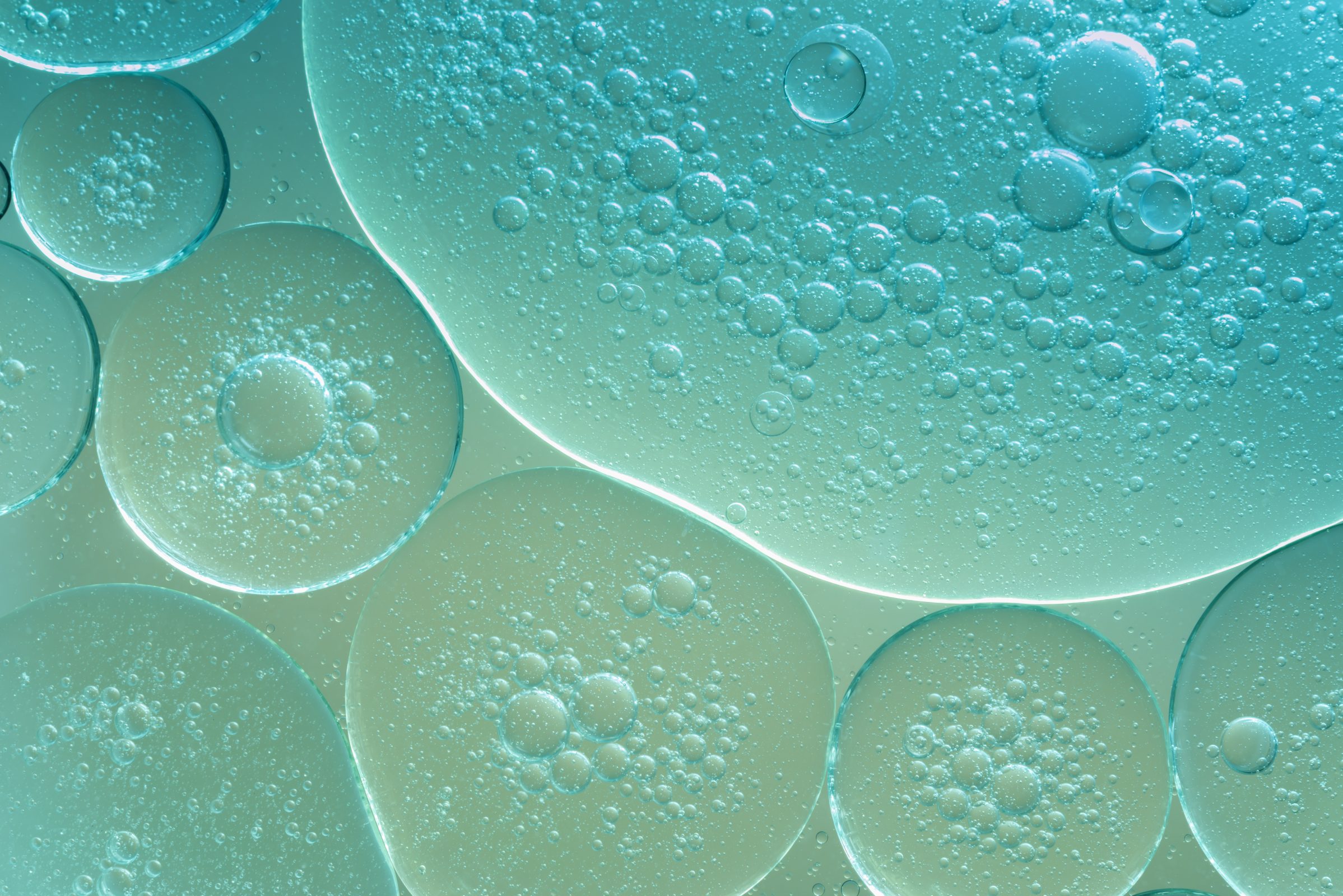
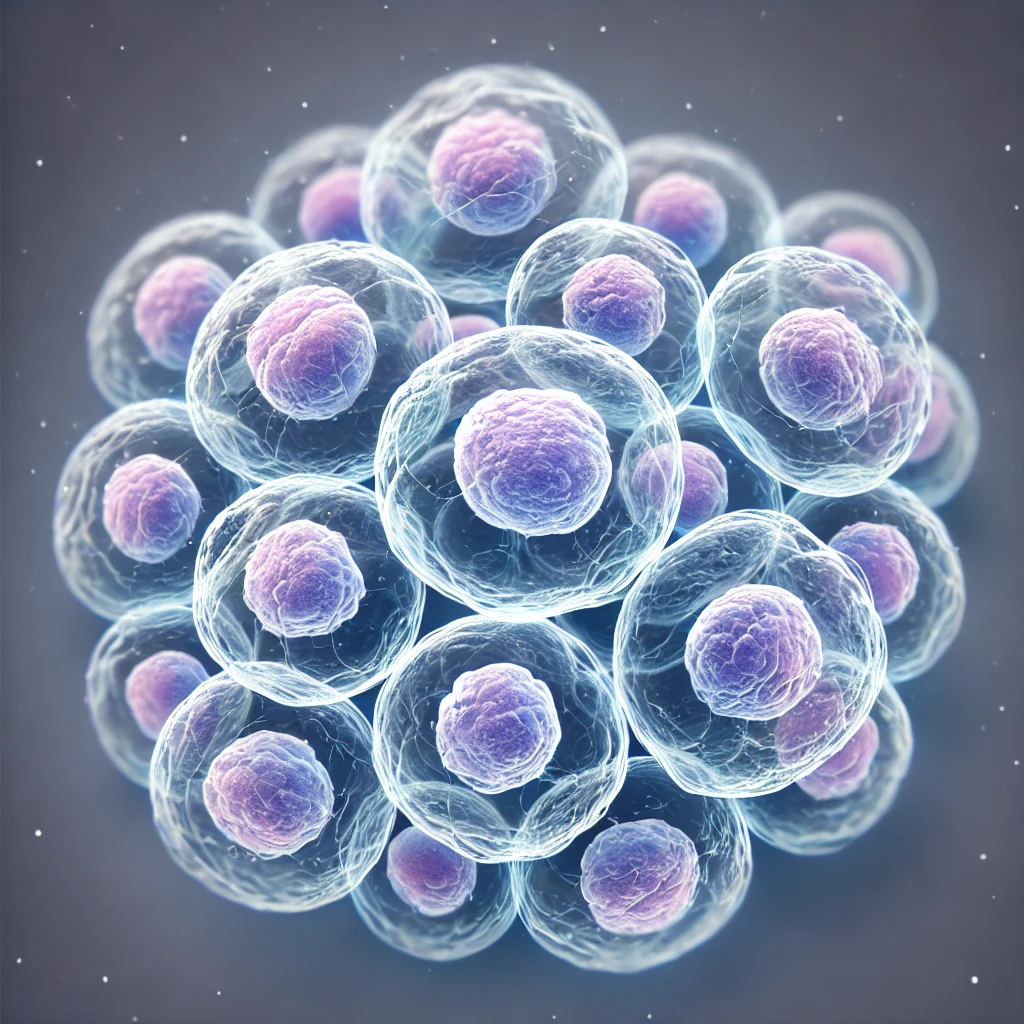
Developing iPSC Therapies: Why Your CMC Strategy Needs to Start Early
Jul 15, 2025
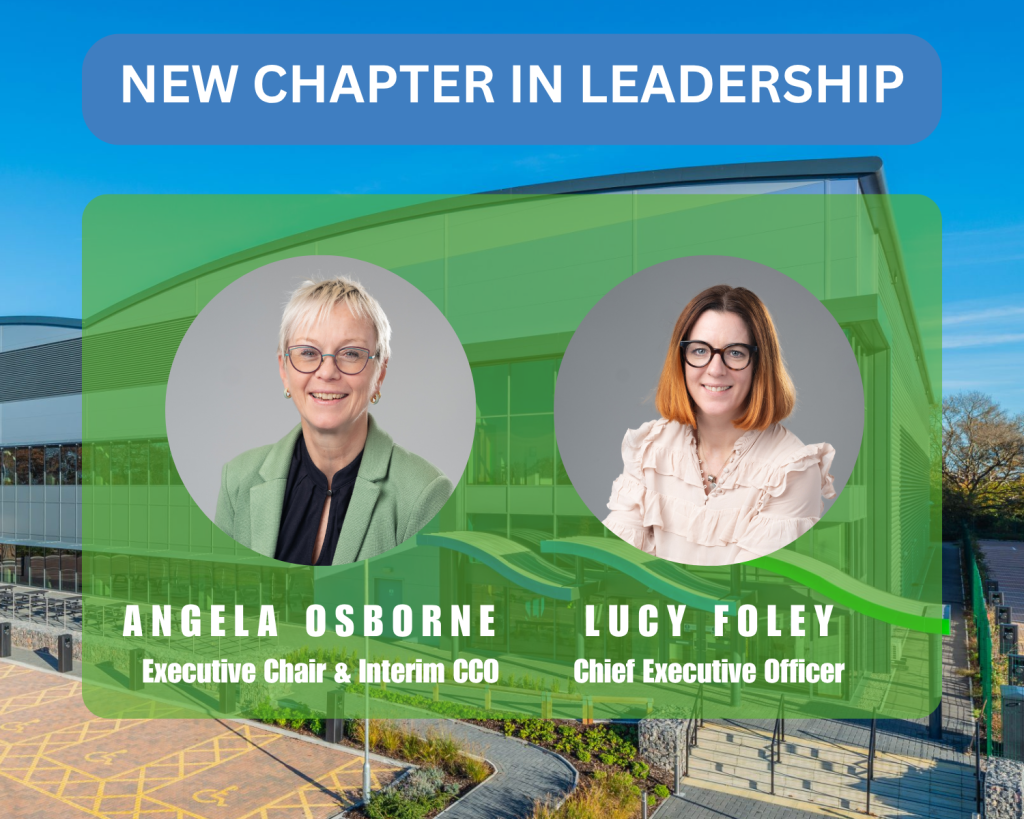
eXmoor Pharma Strengthens Leadership Team with New CEO Appointment
Jul 8, 2025
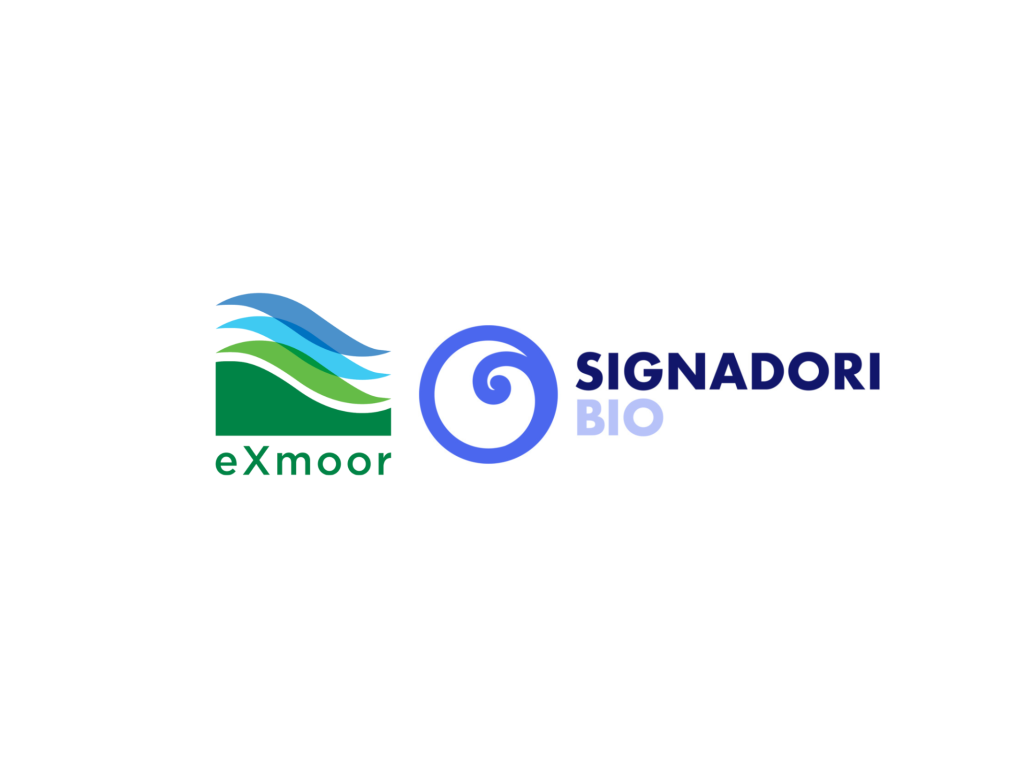
eXmoor Pharma and Signadori Bio launch partnership to develop next-generation monocyte-based cell therapy for solid tumours
Jun 17, 2025
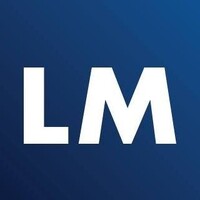
Scaling Gene Therapy Production: From Bench to Clinic
May 30, 2025
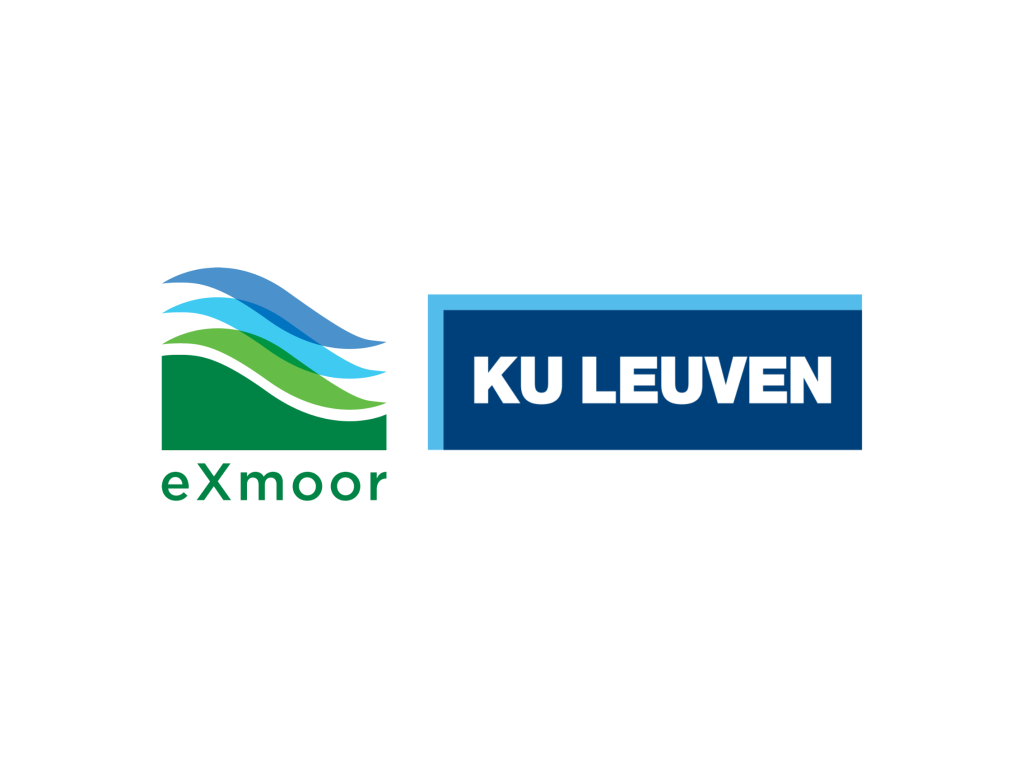
eXmoor Pharma and KU Leuven announce strategic partnership to accelerate cell and gene therapy innovation through new venture
May 13, 2025
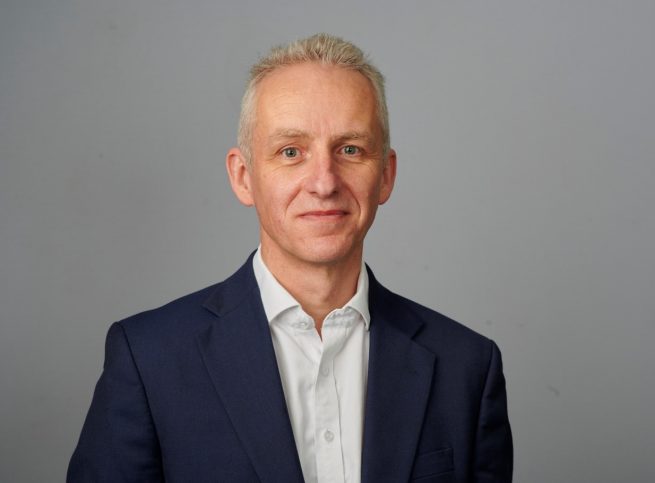
eXmoor Pharma Strengthens Board with Appointment of Dr James Miskin as Non-Executive Director
Apr 1, 2025
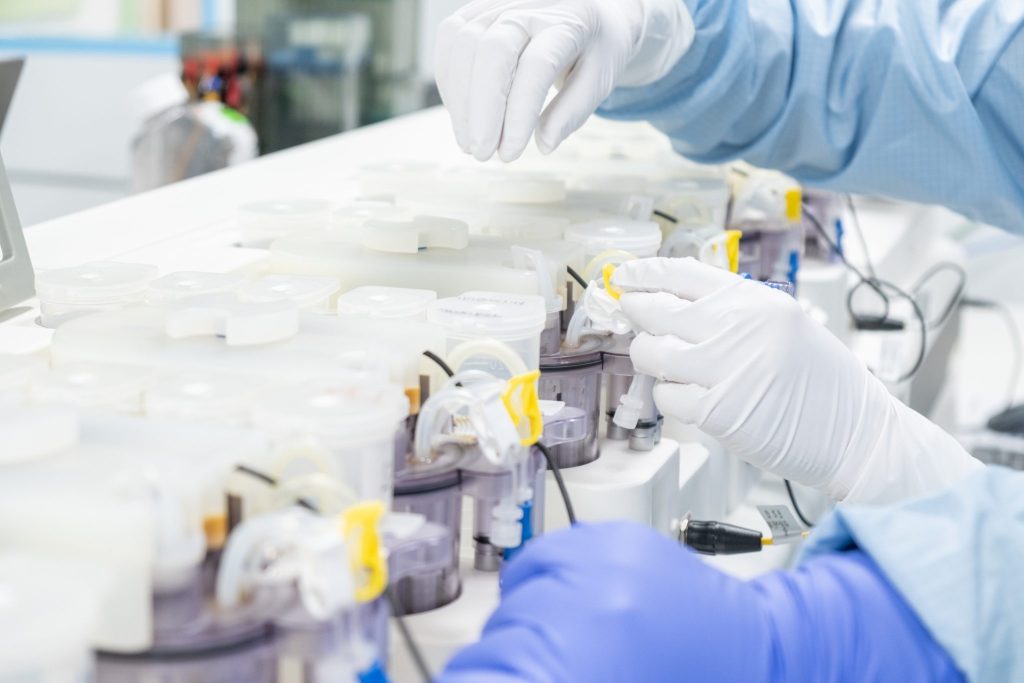
eXmoor and Virica receive funding to improve AAV gene therapy manufacturing
Oct 17, 2024
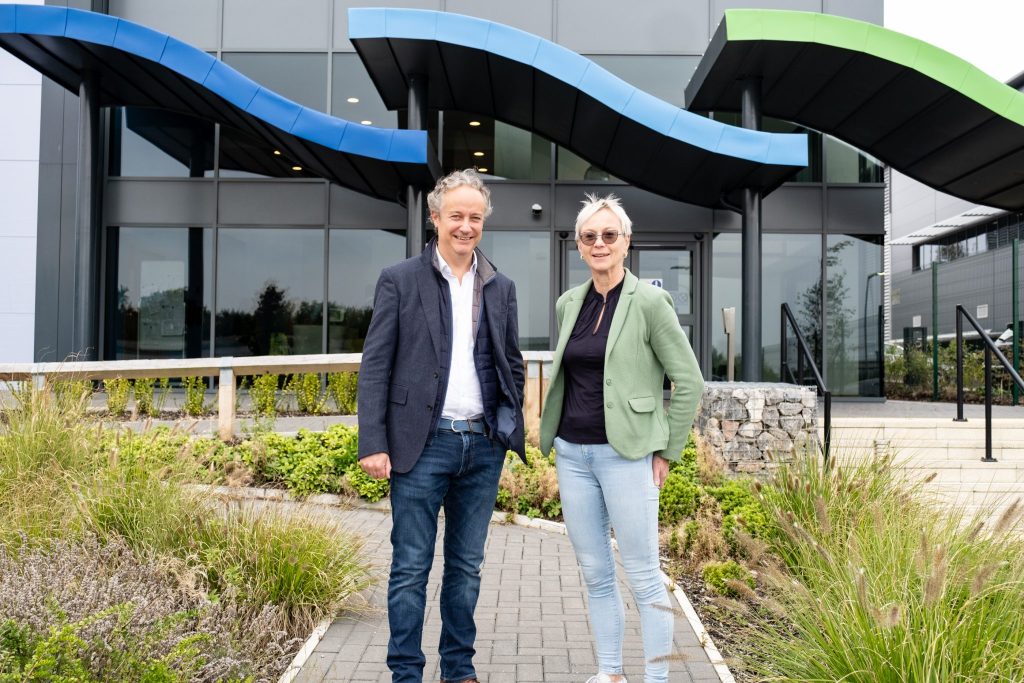
Quell Therapeutics Expands Manufacturing Capabilities for CAR-Treg Cell Therapy Pipeline Through Partnership
Sep 24, 2024
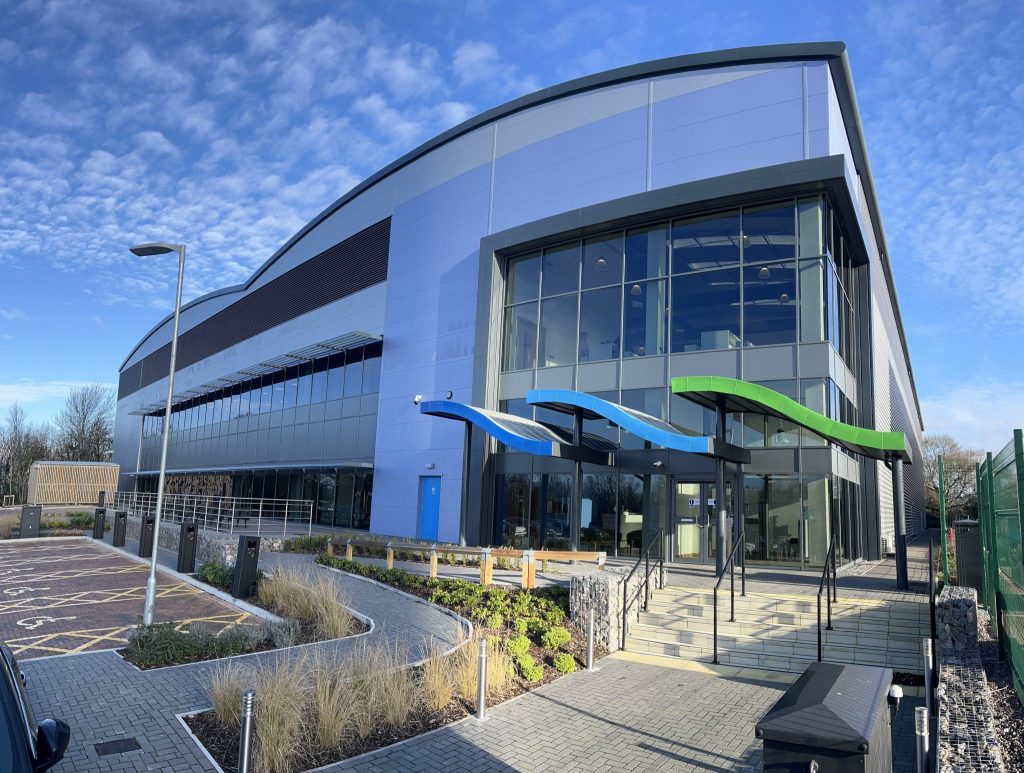
eXmoor Pharma’s GMP cell and gene therapy manufacturing facility receives license from MHRA
Aug 20, 2024
1
2
Stay Ahead with Expert Insights
Join our mailing list for the latest case studies, industry news, and event updates in cell and gene therapy manufacturing.